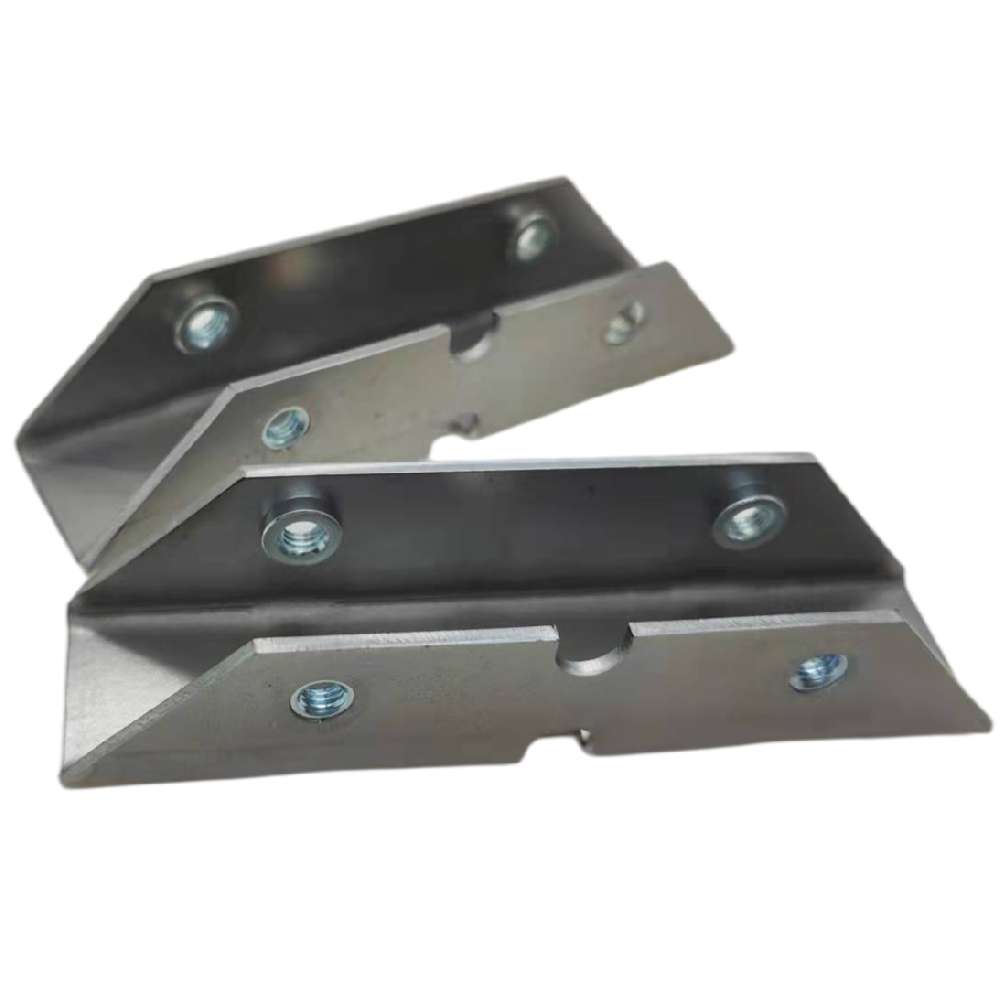
在加工精度和表面粗糙度相同的情况下,孔的加工比外圆面的加工困难,生产率低,成本高。这是因为刀具的尺寸受限于要加工的孔的尺寸,所以刀具的刚性较差,不能使用大的切削量。加工孔时,切削区在工件内部,切削液不易进入切削区,排屑散热。条件差,加工精度和表面质
孔加工方法包括钻孔、铰孔、铰孔、镗孔、拉深、磨削和孔精加工。另外,替代常规钻孔的加工方法是钻深孔和加热。钻孔、激光钻孔、电子束钻孔、电火花钻孔等。不同的零件和材料,不同的尺寸,不同的精度要求,选择不同的工具;不同的效率要求,不同的量产要求,不同的直线度比,不同的加工工艺。
深孔加工
深孔加工是一种以为现有应用设计的刀具为主的加工类型。深孔加工涉及许多不同的行业。今天,该加工领域的成功通常基于混合使用标准和具有设计专用深孔加工刀具经验的专用刀具组件。这些刀具具有带支撑和集成铰刀的加长高精度刀柄,结合最新的切削刃几何形状和刀片材料以及高效的冷却液和切屑控制,可实现最大的穿透力,并在加工安全的情况下获得您需要的高质量。
难点
(1) 不能直接观察切削条件。
(2)切削热不易传递。
(3) 排屑困难,如果被切屑堵塞,可能会损坏钻头。
(4)由于钻杆长度长,刚性差,易振动,孔的轴线容易偏斜,影响加工精度和生产效率。
深孔加工注意事项
(1)深孔加工操作要点:主轴中心线与刀具导向套、刀架支撑套、工件支撑套的同轴度应符合要求;切削液系统应畅通;工件的加工端面不应有中心。钻孔,并避免在斜坡上钻孔;切屑形状应保持正常,避免形成直带切屑;通孔以较高的速度加工,当钻头要钻通时,应降低或停止速度,以免损坏钻头。
(2)深孔加工切削液:深孔加工时产生大量切削热,不易扩散。必须供给足够的切削液来润滑冷却刀具。一般使用1:100乳液或极压乳液;当需要较高的加工精度和表面质量或加工韧性材料时,采用极压乳化液或高浓度极压乳化液,切削油的运动粘度通常选择(40℃)10~20cm2/s,切削液流量速率为15~18m/s;加工直径较小时,选用粘度低的切削油;对于高精度深孔加工,切削油比例可选用40%极压硫化油+40%煤油+20%氯化石蜡。
(3) 使用深孔钻注意事项:
A、工件端面与工件轴线垂直,保证端面密封可靠。
B、正式加工前在工件孔位预钻一个浅孔,钻孔时引导定心动作。
C、为保证刀具的使用寿命,最好采用自动行走。
D、进水口导向件和活动中心支架磨损后,应及时更换,以免影响钻孔精度。